Over Thanksgiving turkey, I explained to more than one family member that the Ford project was going well, and that it is weird to have been working on the car for over a year straight. I've owned the car for almost 20 years now, and though I've undertaken a few major jobs, the car has never been in this state of not-put-togetherness for such a long stretch of time. I mean, even the LS swap back in 2011 only took me about 4 months, and that was probably the biggest change to date. To have been working in earnest on the car since last October and still see this:
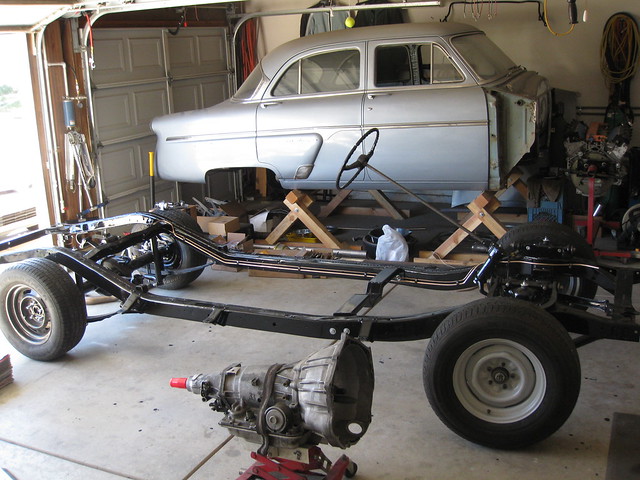
when I step out the garage door is a little weird. And troubling. Maybe a little scary, like I'm in over my head.
Maybe I just need to stop watching TV shows where the cars get completely redone in 2-4 weeks. Even though I know it's fake, and they have a ton of guys working on the cars day and night, it still leaves me feeling like I'm making very little progress.
Anyway, even if the progress is a slog lately, things are still happening. As my neighbor with an unfinished '50 Chevy pickup in his garage reminds me from time to time, as he stops by to shoot the breeze, at least I'm still in the mood to work on the Ford. Strike when the iron is hot, and all that jazz.
I spent a fair amount of time bending up and installing the brake and fuel lines back in late October. The old lines were looking pretty bad and probably full of crud, and I wasn't about to put them back on the pretty frame. I bought some NiCopp line to use after reading very good reviews about the stuff, and overall I'm pretty happy with it. Being a mix of nickel and copper, it is easy to bend and will never rust. Cost-wise, it wasn't much more than stainless steel. The brake line was a piece of cake to fit, but my only problem was trying to bend a 90-degree angle on the 3/8" fuel line. The sidewall isn't very thick, and the material is so soft that I couldn't get more than about 70 degrees before the tube started to kink and flatten out. I was using a good tubing bender and everything - I even tried filling the tube up with sand to hold the shape. That helped, but I guess I couldn't pack in in there tight enough to keep from shifting and compressing as the tube bent. In the end, I wasted a pretty long stretch of fuel line and then redid the whole thing with different routing, including as few sharp bends as possible. That meant running the line inside the frame rail instead of outside, which is visually better but isn't the way the stock line ran and put the line on the same side as the exhaust. I think it'll be fine, though.
One thing I'm really happy with is the type of line clip I found at Summit. They're super-hard nylon, black like the frame, and came with stainless fasteners. Also, they were cheap. I have zero complaints about them and will definitely use them again in the future.
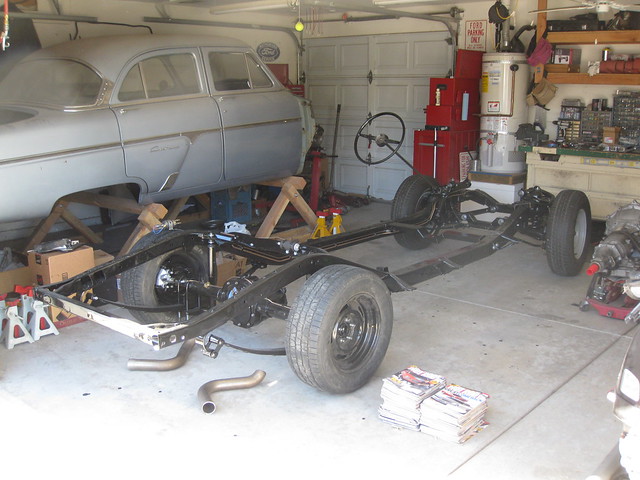
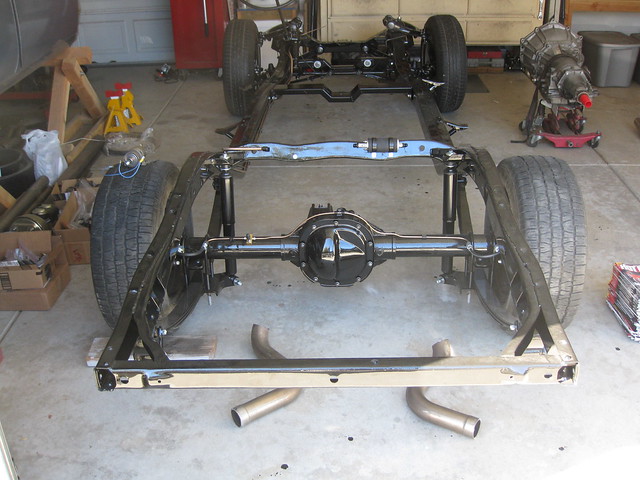
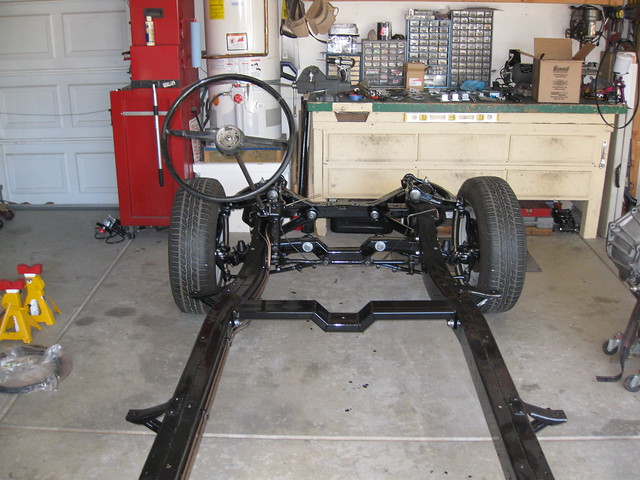
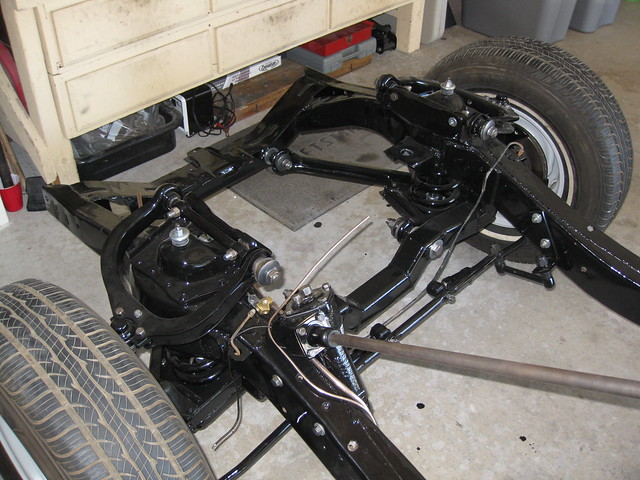
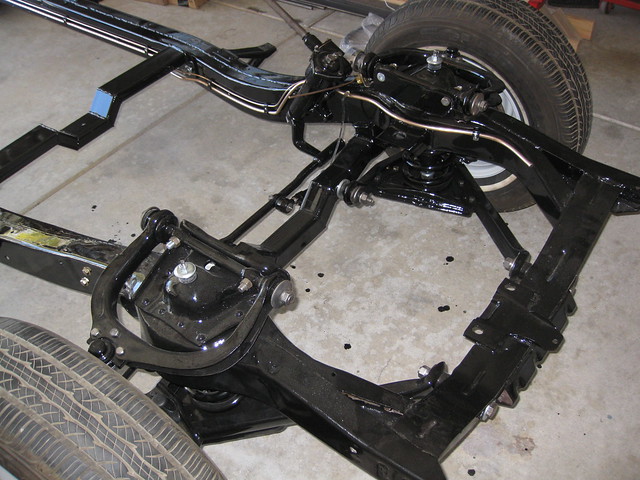
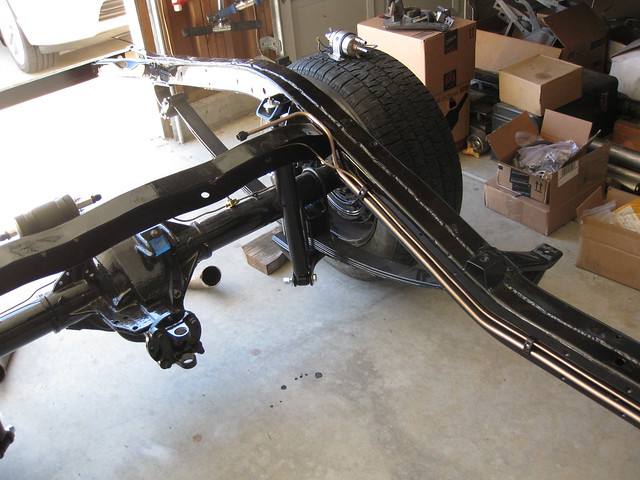

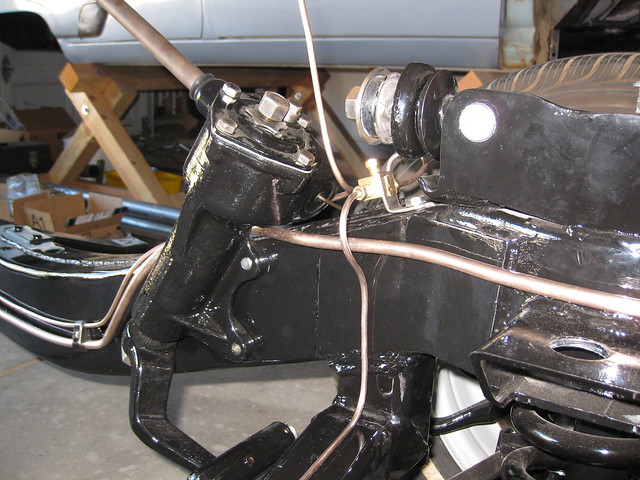
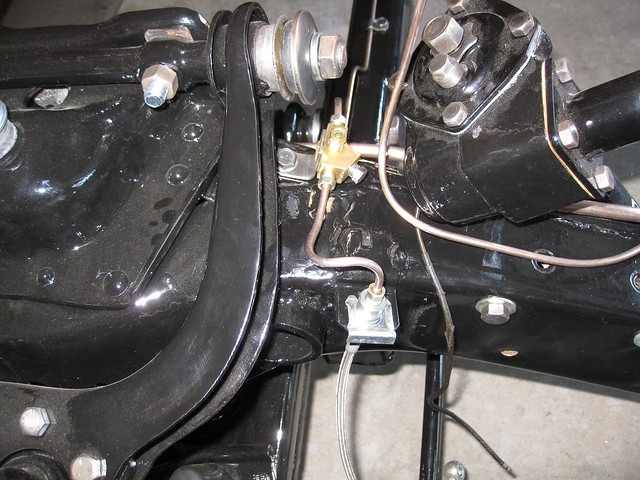
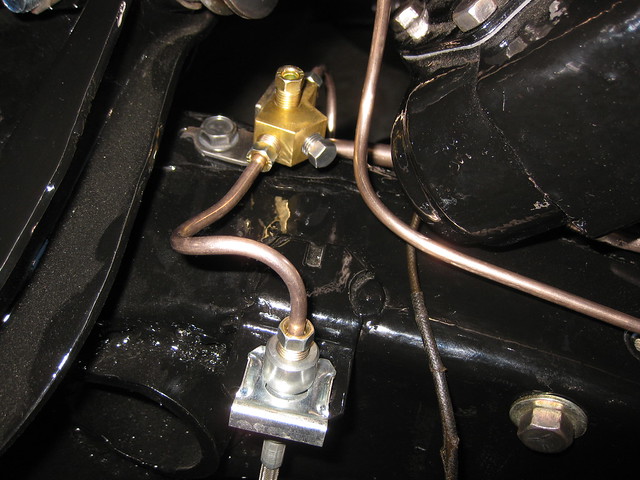
