Work on the rearend, that's what. I've been staring at this Explorer 8.8" rearend for months now, and I'm finally at the point where I can do something with it.
The first order of business: modify the Explorer shock mount/u-bolt bracket plate thingies ("plates," from this point on) to work with the narrower '54 springs. Two differences between the original Ford and new Explorer setups are a larger diameter axle tube (3.00" old vs. 3.25" new) and larger leaf spring width (2" old vs. 3" new (actually, the Explorer might be 2.5", but it doesn't really matter)). I know the plates could work without modification, as my dad just put an Explorer rearend in his Chevy and didn't change anything. However, because I know the extra gap between the u-bolts and leaf springs will eternally bother me and because I am in a welding kind of mood, I decided to mess with them a bit.
I started by welding the factory holes closed.
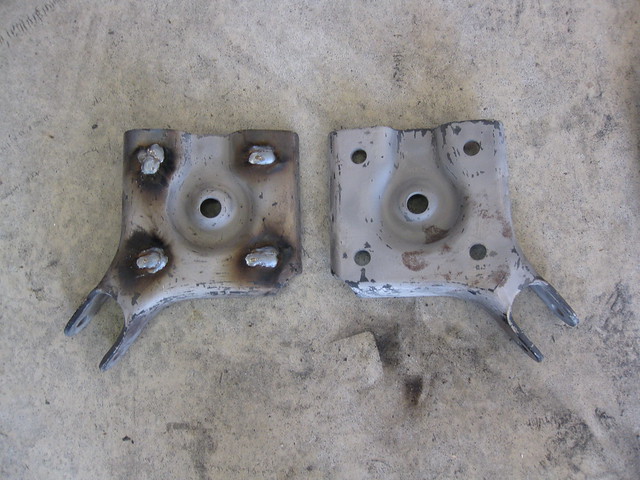
Then I ground them smooth and realized that the "dip" or "valley" at the back of the plates is wide enough that they might shift around on the narrow Ford leaf springs. I cut a few pieces of scrap metal to fill the valley, welded them in quickly, not caring about appearance for once, and then dressed the welds on the top to get the spring mounting surface fairly flat.
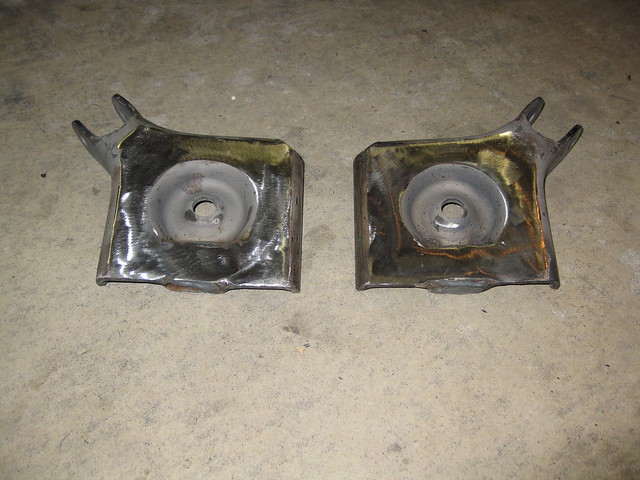
I spent more time than I expected laying out the hole pattern to drill. It's tough when none of the plate edges are square or even straight, and I ended up measuring out from the center of the middle hole.

The u-bolts are 1/2" thread and will be spread apart 3.25" inches, so those holes were easy to locate. The distance between each pair of u-bolts was trickier. I was going to leave exactly 2 inches of room, since that's how wide the leaf springs are and the whole point of this exercise is to take up all slack in the assembly. Fortunately, I didn't start drilling at that point. First, my lowering blocks are wider than 2 inches. Second, the leaf spring perches that I will eventually weld onto the axle tubes are even wider than the lowering blocks. When everything was accounted for, I coincidentally wound up drilling the holes 3" apart on center, which is exactly what the original '54 plates were. There's definitely a gap on either side of the leaf spring, but that's how it looked on the old rearend and it worked just fine.
I drilled the holes, put one side of the suspension back together for mock-up, and bolted the plate in place. Obviously, the leaf spring in the pictures below isn't put together correctly. I had the long spring hooked up over the weekend when I first slid the rearend in place, and tonight I just threw the extra springs back in there to give me the right thickness. The first few pictures are from the weekend, and the last two are from tonight.

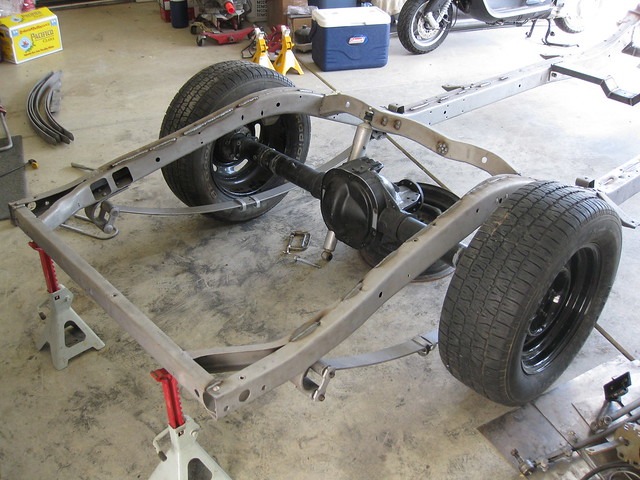

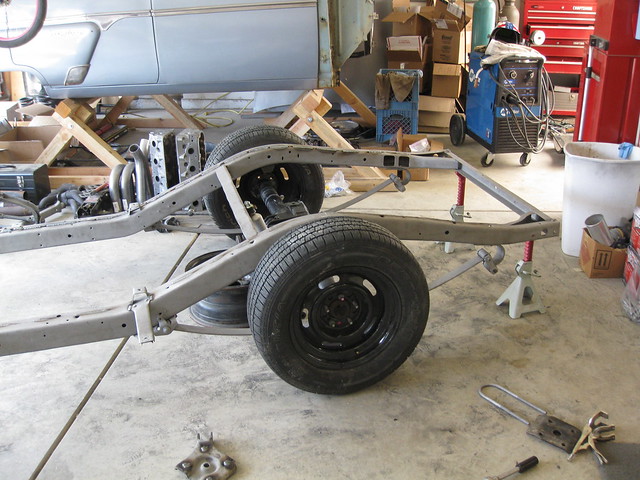
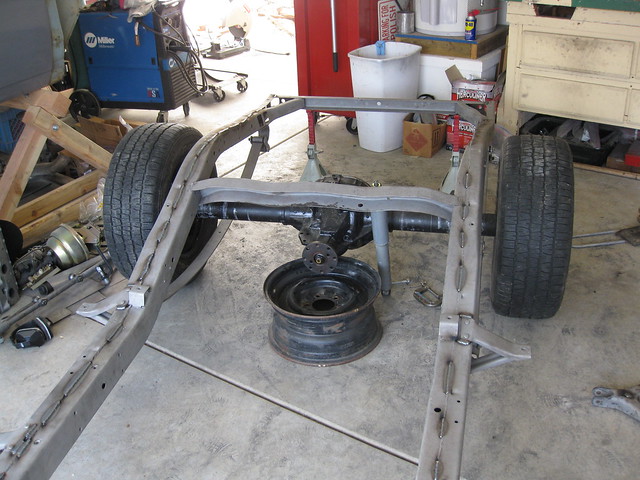
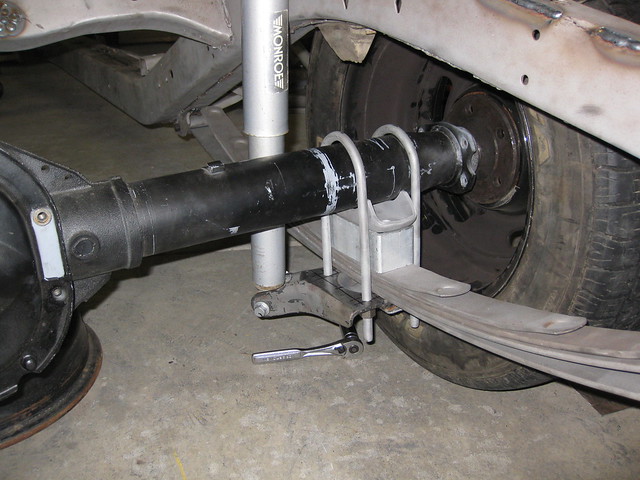
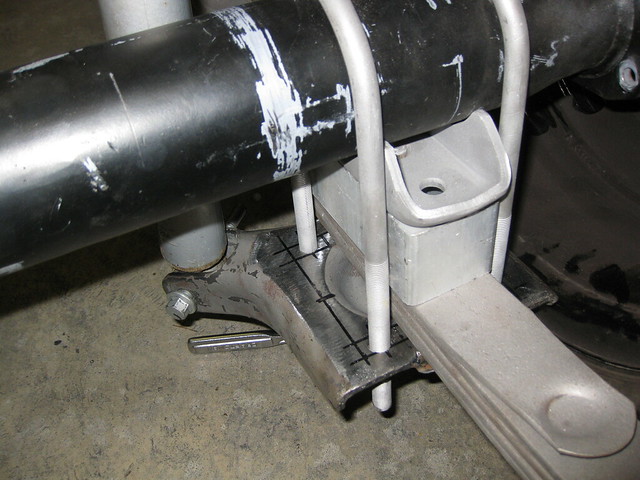
No, those aren't the wheels and tires I'm going to use, although it would be nice to get a tire that wide in there. Those are my dad's old tires on some new universal bolt-pattern GM Rally wheels, which my dad scored at a tire shop for 100 bucks (!). He went in to get his new tires mounted on his first set of brand-new Rallys, purchased from Summit for about $300, and the guy at the shop told him about this other set. It was a bummer than he already spent the money at Summit, but he bought the second set from the guy anyway because it was a killer deal and he knew I needed a set of wheels to roll Maude around on for the time being.
That's as far as I made it today. This weekend I hope to get the other plate done and make some upper shock mounts. If I have time I will start working on the motor mounts, too.