Let me muse about that for a minute, if you don't mind.
Used to be, I'd get the flu and it was no big deal. Miss a few days of school when I was a kid, a few days of work after that, play video games, watch movies, no big deal. As long as I had DayQuil and Kleenex around I was fine.
Now I'm 35, which I know is not "old." But it's old enough that I realize I'm not young anymore. Case in point: I got the flu in December 2012 and I thought I was going to die. It's not the coughing or congestion that wrecked me back then, it was my body's total inability to regulate temperature, combined with debilitating aches. I literally spent about a week in bed, alternately sweating and shivering uncontrollably while my knees and hips and ankles throbbed in pain.
Now, on the bright side, I haven't been sick since then. I think there was a stretch of time when I got sick a few times a year because I wasn't very active. These days I spend a few days a week playing softball with my friends and baseball with my son, I walk around a lot on my breaks at work, and I am always out in the garage - not necessarily working up a sweat, but definitely moving around outdoors and staying active.
But all good things come to an end, right? For me, the beginning of the end started when my son got sick two weekends ago. Then my daughter and I started feeling lousy mid-week. The other weird thing about getting sick at this point in my life is that I can't always stay home in bed. This week, it wasn't that I didn't have the leave time available to me. It was that I actually had responsibilities at work that I couldn't delegate or blow off. I sucked it up on Thursday and Friday and went to work because I had things to do, and it went okay. But it was just postponing the inevitable.
I had a 3-day weekend (Why, you ask? CA State employees enjoy more holidays than pretty much anyone else). Today is day 3, it's sunny outside, the wife and kids are at work and school, and I'm sitting on the couch typing instead of going outside to work on the Ford. I spent the last two days sweating and shivering again while my joints protest against every movement I make. This morning I woke my wife up because I was shaking the bed so hard. I'm miserable, and I wasted the whole weekend.
Getting old sucks.
Anyway, here's the last work I did on Maude. I'm working on reinforcing the frame in places where it appears necessary to me. The old crossmember holes are the obvious points, but I'm trying out a plan for the upper A-arm mounts that will hopefully allow me to remove some more of the stock material, which, in turn, allows more header clearance. It's one of those things that I am doing now while I have good access, even though I probably don't need to do it at all.
I used 1/4" steel plate for the A-arm job. Here's a before and after.
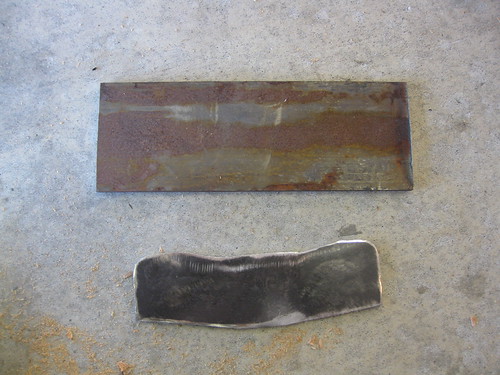
I've seen lots of guys lately doing custom A-arm setups for airbags and such where the only mounting point for the upper arm at all is a vertical piece of plate, probably 3/8" or so. If that's all you need (instead of the stock Ford "hat" in all its obtrusive glory), then my idea for welding 1/4" plate up against the existing 1/8" hat should be plenty strong. This will hopefully make more sense when I get around to welding everything together and then grinding the hat down flush. I will naturally post pictures of the finished product eventually.
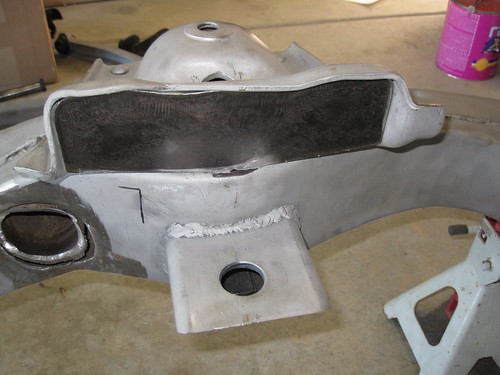
I used 3/16" plate to cover the old crossmember holes. I would have gone bigger, but of course the frame curves right here so I needed my plates to curve as well. I wasn't sure I'd be able to bend 1/4" with my limited tools, and the stock frame appears to be 1/8" thick so 3/16" is at least bigger than that. This stuff was tough to bend as well but a MAPP torch and a BFH eventually did the job to my satisfaction.
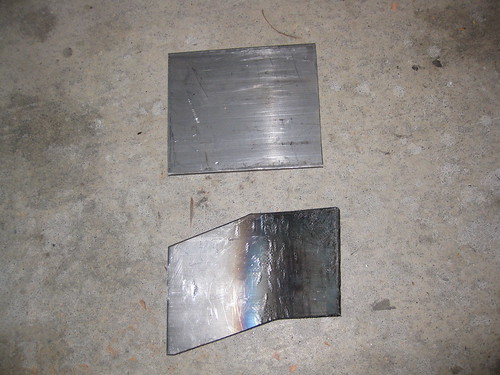
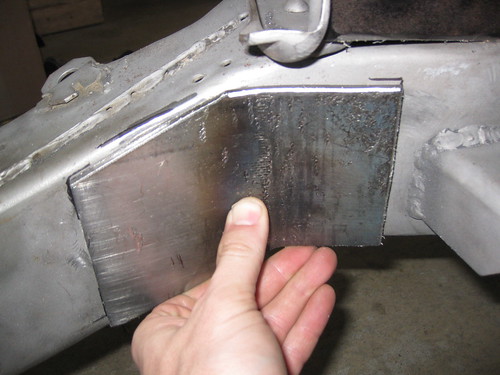
Tacked in place.
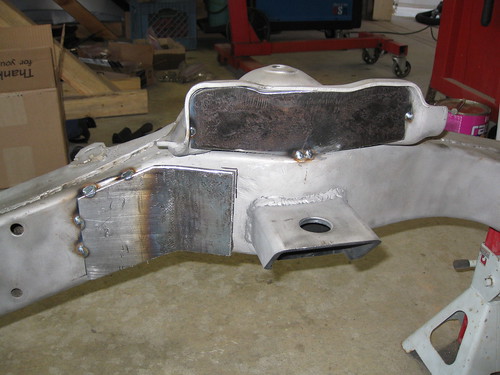
I'm trying to be smart and only tack weld things for now, welding just enough for structural stability but leaving myself an easier job of cutting things apart if they don't work out. In the past I used to just burn things in right away because I got excited (motor mounts, for example), but after the nightmare of removing some of those things (motor mounts, for example) I think I learned my lesson.
Maybe tomorrow I will write another post about the motor, which is mostly put together again. Stay tuned.